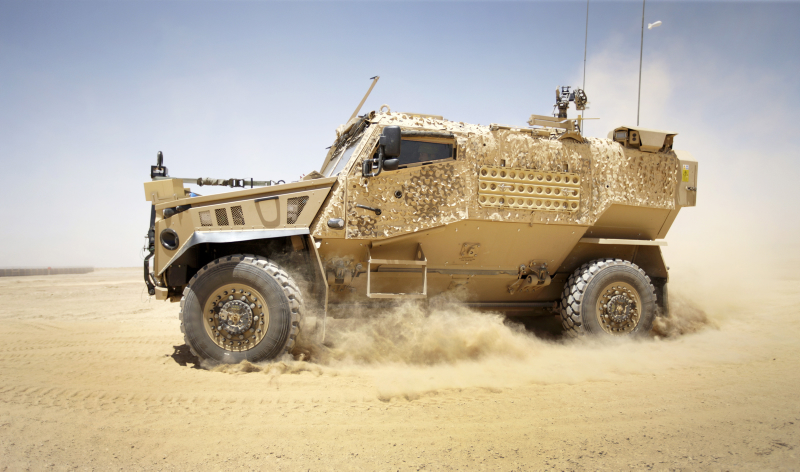
Despite the cold, I was excited. It was the first day we got to explosively test the prototypes that British industry had been developing, for what would soon become the Foxhound vehicle.
The weather in the Northumbrian hills was below zero and the runoff from the fields had scattered the untreated road with icy patches. When I arrived at the test range, bundled up like a high-vis Michelin man, there would follow many hours of preparation, preceding the few milliseconds of blast-testing.
When blowing up vehicle prototypes that cost six figures, you don’t want too many surprises on the test range. And this is where I come in ….I run a small team at the Defence Science and Technology Laboratory at Porton Down – the top defence lab and home to a wide range of expertise including material scientists, mechanical engineers and physicists who engage in research and development into new armour systems to protect vehicle crews and dismounted troops on operations. My team focusses on understanding the way new armour technology protects vehicles’ crews from Improvised Explosive Devices (IEDs). Our aim is to develop new protected vehicles quickly, with the minimum expensive and time-consuming trialling.
With Foxhound, before the prototypes emerged, with their prominent v-shaped hulls, my team had already conducted model-scale experiments to quantify the reduction in momentum imparted to the hull. This allowed us to predict Foxhound’s performance prior to its testing. The seats and harnesses had also been extensively tested in lab-trials to demonstrate their ability to isolate the crew members from the vehicle’s acceleration and stop them being thrown from their seats and around the vehicle’s interior. The name of the game is to understand the performance of protected vehicles as early and in as much detail, as possible.
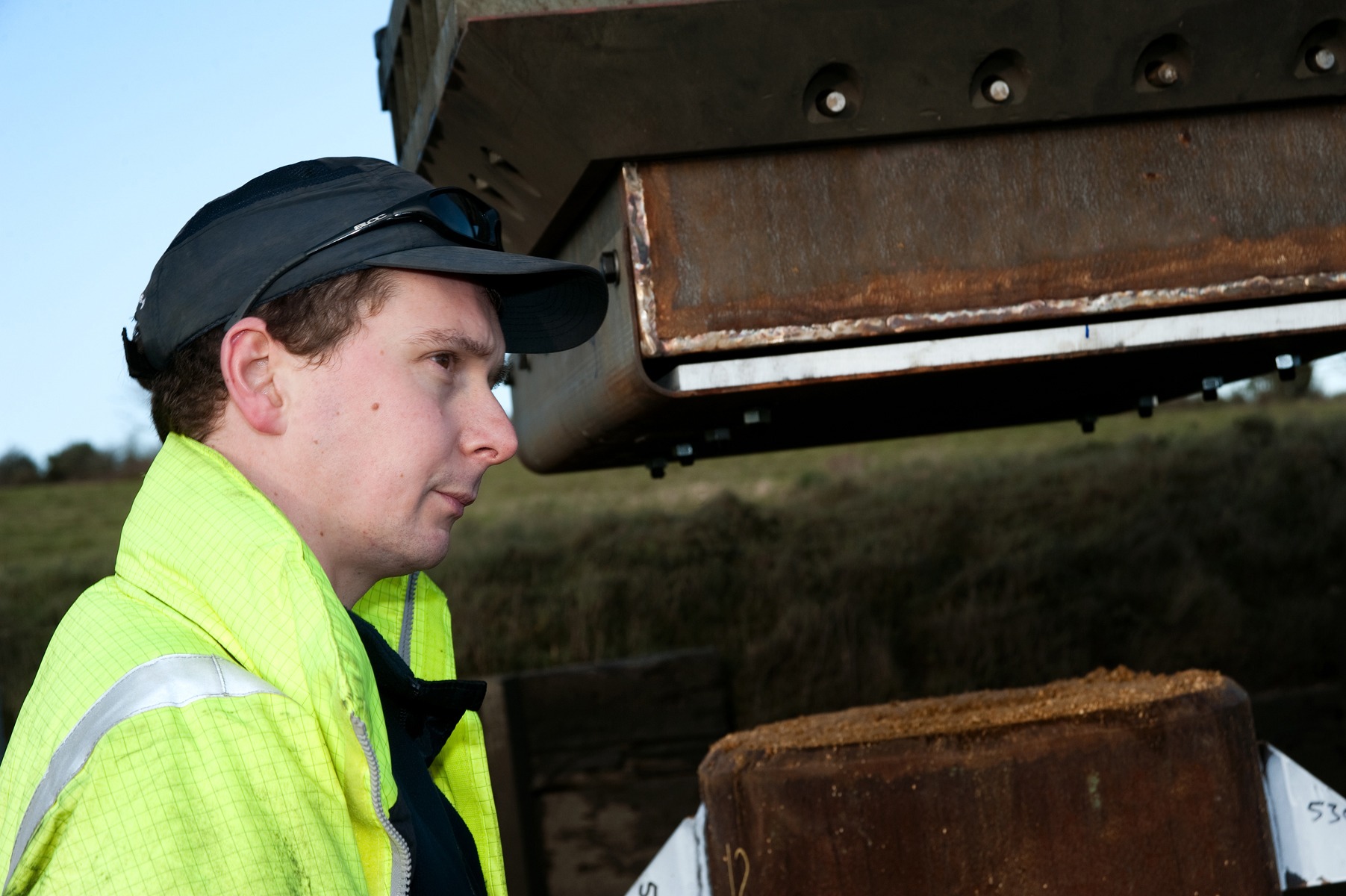
This continues when vehicles enter service. I have spent a lot of time on the phone to deployed personnel in Afghanistan advising on what each vehicle can and cannot safely do. This can be relatively genteel, such as preparing briefings for visiting TV crews, or laden with sadness when I have to investigate the circumstances around IED-related fatalities. I firmly believe that we owe it to the victims of such tragedies to learn from these events and take steps to reduce the chances of the same circumstances reoccurring. Even as IED sizes have grown in recent years, British protected vehicle technology has risen to the challenge and I am proud that I have been part of this process.
Even as combat operations in Afghanistan end and troops return home, my work does not end. I am looking forward to exploring more novel ways to provide protection in ever lighter armour solutions that weigh vehicles down less and leave them with better mobility levels. With more time to invest in higher-risk ideas, I think we can take great steps forward. We have recently completed a project looking at novel materials to enhance the protection of armoured vehicles. While we still need to check that the materials are robust, waterproof and wear resistant, I am enthusiastic about the possibilities that tomorrow brings.